An ISO:9001 Company
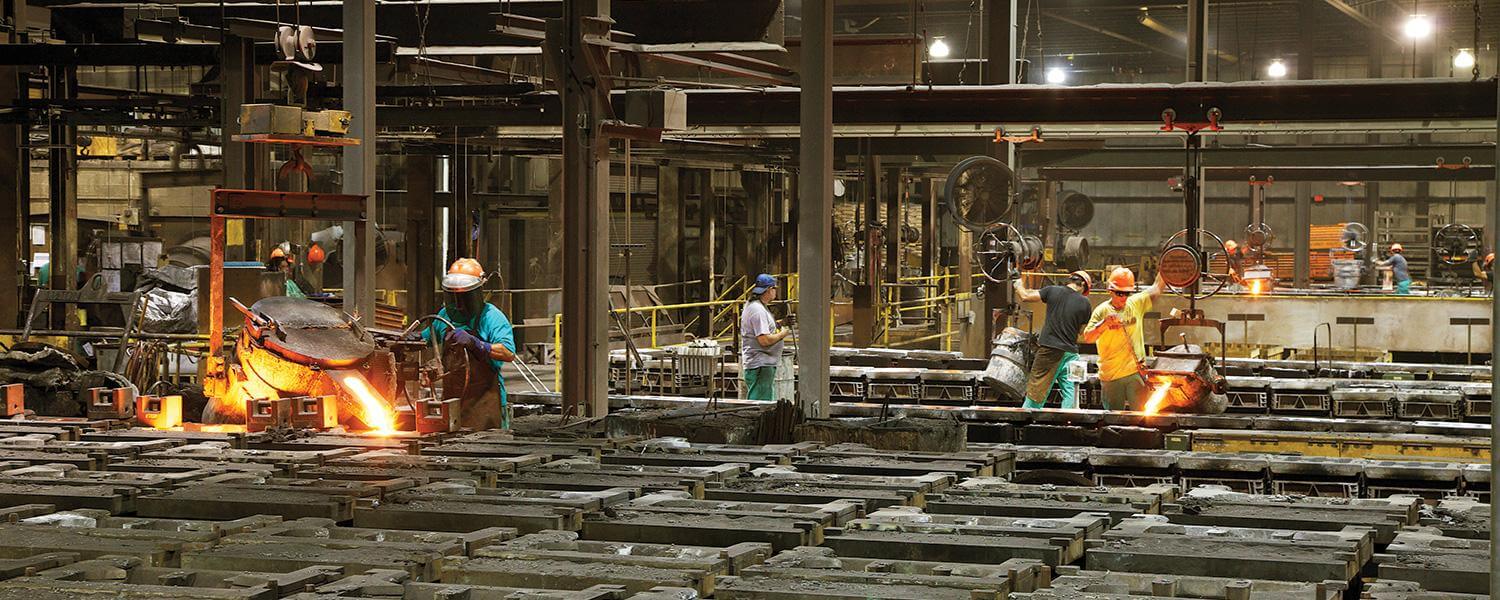
Pouring Iron on Six Automatic Molding Centers
PEOPLE
- 250 Employees
- Professional Management Team
- Highly Skilled and Qualified Technical Staff
- Productive, Motivated Craftspeople
FACILITY FEATURES
- 225,000 square feet of manufacturing space all reconstructed in the past 30 years with high bays, insulated roofs and modern lighting
- Discovery Center
- Training Facilities
- Multiple Conference Rooms
- 200+ acres of land
PRODUCTION CAPABILITY
- Medium and high production capacity in casting sizes from 1 to 250 pounds
- Capacity of 30,000 tons per year of finished castings
- Reliable physical properties and consistent microstructure
- Complete pattern layout and design capability
METALS CAST
Gray Iron
Class 25,30,35,40 tensile and heat resistant irons SpecificationsDuctile Iron
Grades 60-40-18, 65-45-12, 80-55-06, 100-70-03 & 120-90-02 SpecificationsAustempered Ductile Iron
Grades 110-70-11, 130-90-09, 150-110-07, 175-125-04, 200-155-02 & 230-185-01 SpecificationsSCHEDULING
- Computer integrated throughout the casting process
- Centralized, accountable and easily accessible
- Average 97% on time when measured against the customers’ delivery window
- Customized software; Our software fits our process
PATTERN MAKING
- Complete pattern layout and design with many up-to-date pattern shops at our disposal
- Solid Works
- Magmasoft solidification software
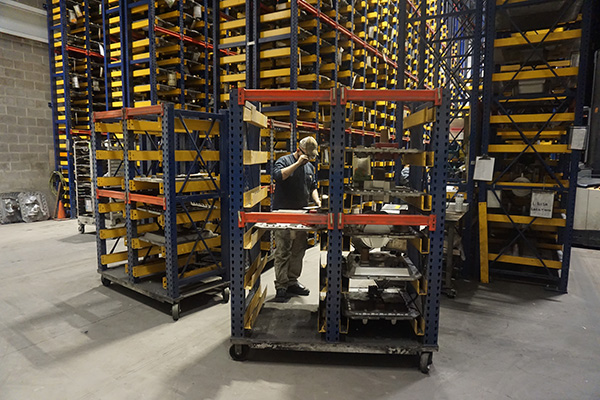
Pattern Storage Area
CORE PRODUCTION DEPARTMENT
- Cold-box and shell processes
- Three Gaylord 24-VSTB
- Two Gaylord 19-VSTB
- One Gaylord SATB-15
- One Laempe LB25
- Two Laempe LL20
- Four Beardsley & Piper SF 6
- Two Beardsley & Piper 104
- Intricate core assembly capability
- Digital images with computerized detailed instructions for all assemblies
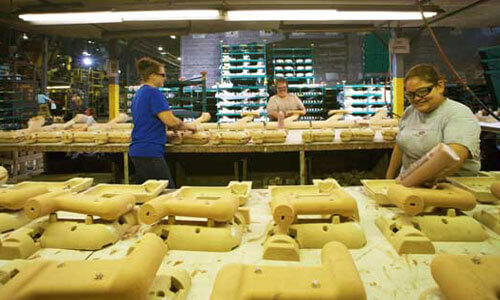
Core Assembly Area
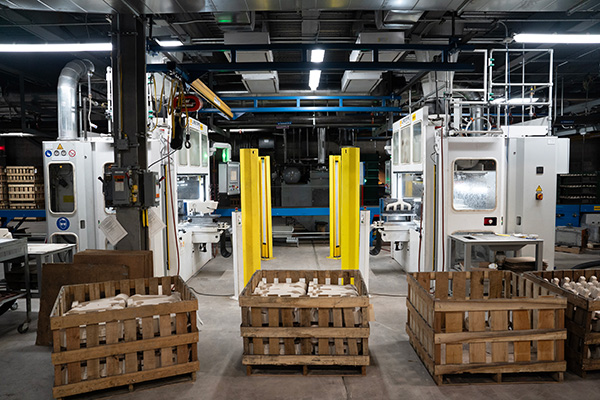
Two Laempe LL20’s
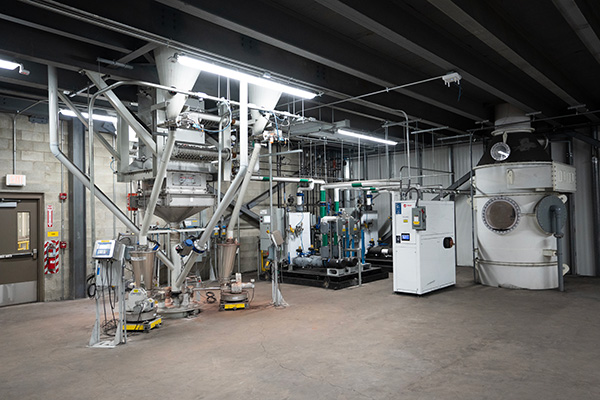
Sand Additive Weight Deck
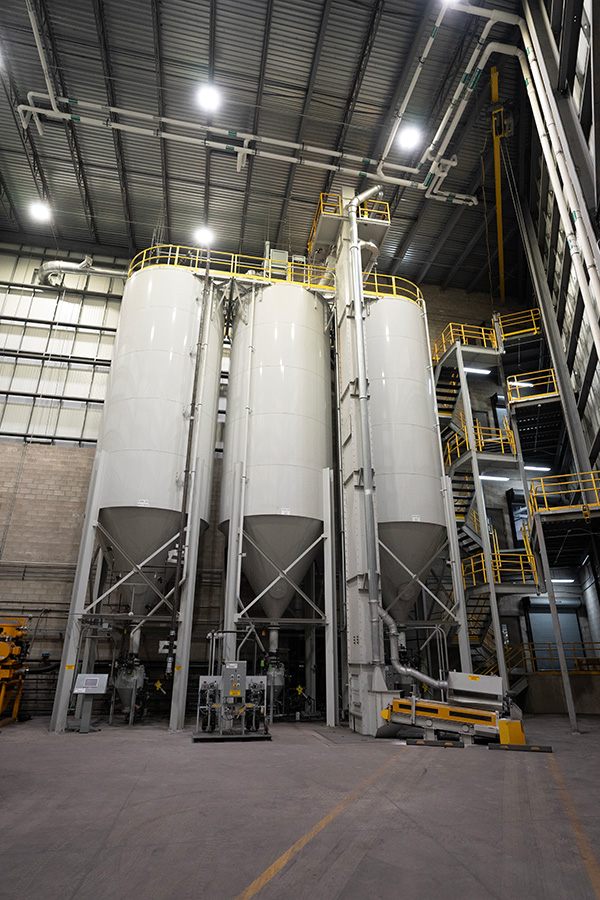
New Sand and Bentonite Storage Silos
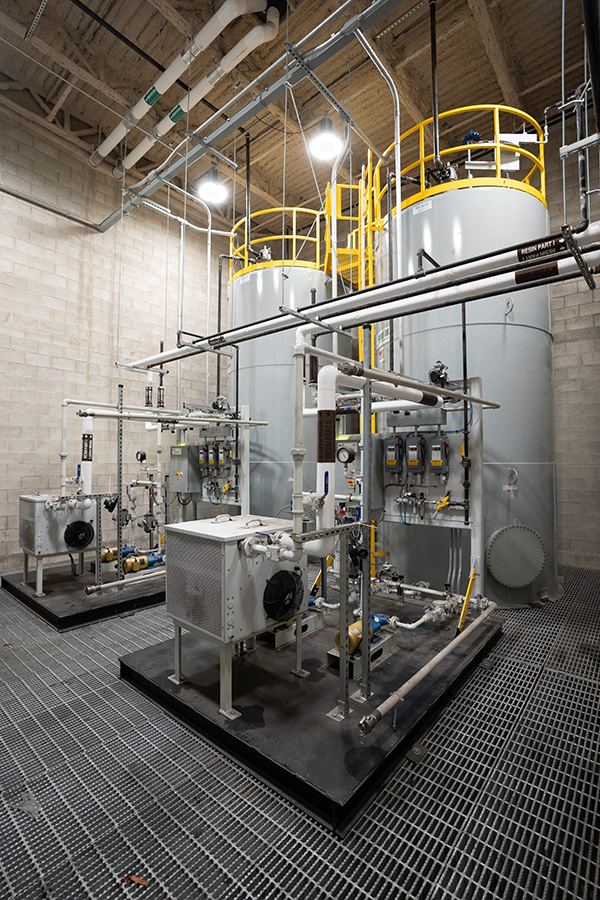
Resin Storage Tanks
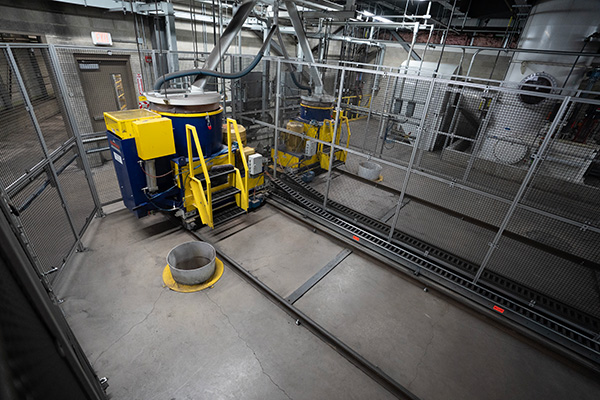
Two Sand Batch Mixers
MOLDING DEPARTMENT
- Automated Sand Preparation with two B&P 100B-250 muller’s with Hartley Controls
- One DISA 28 x 32 flask with a 14″ cope and 12″ drag adjustable down to an 11″ cope and 9″ drag
- Two DISA Match 130, 20 x 24 flask with an 8″ cope and 8″ drag adjustable down to a 6″ cope and 6″ drag
- One Hunter 20 x 24 flask with an 8.5″ cope and 7.5″ drag
- Two Hunter 14 x 19 flask with an 5.5″ cope and 4.5″ drag
- Extended cooling lines available to accommodate heavy section jobs
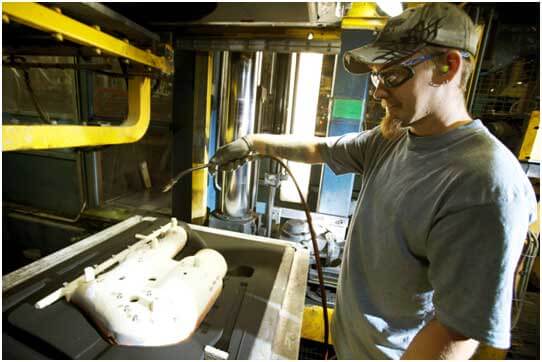
DISA 28×32 Molding Machine
MELTING DEPARTMENT
- Two 10 metric ton medium frequency Inductotherm furnaces with a 7,000KW power pack and Meltminder controls
- Two 4 metric ton medium frequency Inductotherm furnaces with a 2,500KW power pack and Meltminder controls
- Tight chemistry control with complete traceability
- Excellent, documented temperature control
- 300-Ton-Per-Day melt capacity
- Customized Energy Solutions energy management software with Demand Control and Demand Response features on the furnaces
- Emergency Load Response Program and Synchronous Reserve Program participant to reduce stress on the PJM grid
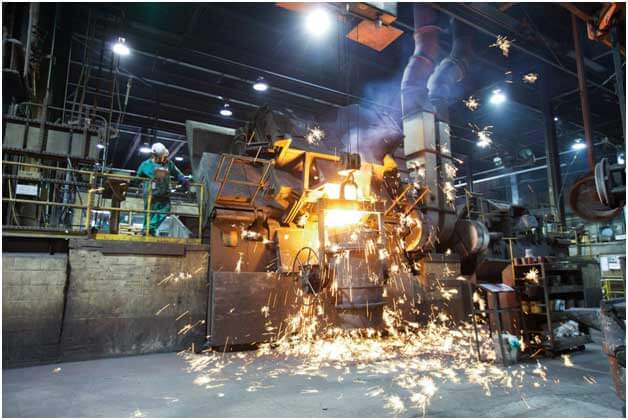
Tapping Iron from 10 metric ton furnace
FINISHING
- Eight Foxall robotic grinders
- Four Fox stationary grinders
- Two floor grinding stations
- Two 34-cubic-foot BCT Tumble Blasts
- One 21-cubic-foot BCT Drum Blast
- One BCT Spinner Hanger
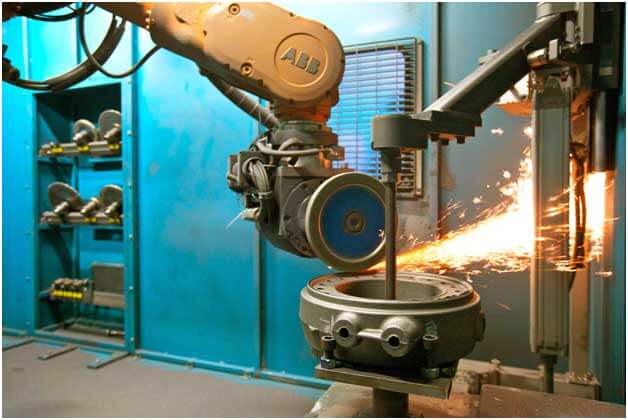
One of Eight Robotic Grinding Cells
LAB
- Microscope with Automatic Image Analysis software
- Coordinate Measuring Machine
- Romer 3D Scanner
- Bore scope
- Spectrometer
- Leco Carbon/Sulfur Determinator
- Leco Oxygen/Nitrogen Determinator
- PPAP’s
- Chemical certification
- Physical certification
- Metallographic reports
- Letter of Compliance
- Complete, electronic sand lab
- Computerized, customized and completely integrated scrap reporting
- Newage automatic hardness testing machine