Benton Foundry is a casting house committed to environmental initiatives and ensures eco-friendly casting operations through various additions and improvements. Our facility does not have steam plumes nor smokestacks, and all our cooling systems are either closed-loop poly-glycol cooled systems or air-cooled systems. There is no discharge water from our operations.
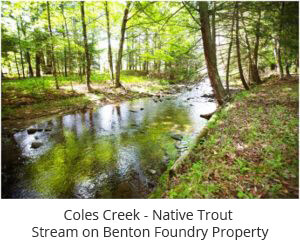
An example of our commitment is the reconfiguration of all control points to ensure that all products of combustion are consolidated into one collector, while the other collectors are used for polishing and re-circulating the air. This system upgrade included the addition of a dust collector with an airflow of 120,000 CFM, featuring a 500HP Baldor Super E (Energy Efficient) motor with a variable frequency drive and a broken bag detector operating off magnahelics. During the winter months, the system recirculates the tempered, clean air back into the facility through prefilters and HEPA filters. This air is used for heating purposes, as well as reducing the negative pressure in the facility. In the summer months, the warm air is directed outside. In addition to the environmental benefits of this system, the pouring deck is remarkable for its lack of smoke. This tempered, clean working environment also results in a six-figure heating cost reduction that, in effect, pays for the system.
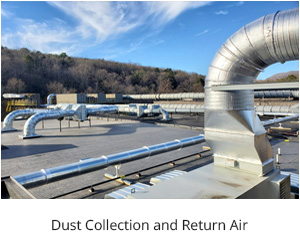
The second phase of this project included another dust collector featuring a 200HP Baldor Super E motor, variable frequency drive, broken bag detection and a lime injection system to increase the life of the bags. This dust collector has a flow rate of 60,000 CFM and is used to collect products of combustion from the furnaces, pre-heaters and sand systems. The products of combustion are filtered prior to discharge. This voluntary initiative reduced the discharge levels on the new collectors to the BACT (Best Achievable Control Technology) Levels of less than 0.005 grains/SCF. This was a cooperative effort between Benton Foundry and PA DEP to permit Benton’s five-year expansion plan under one permit. The result was a voluntary 67% reduction in emissions.
The third and fourth phases of the project have added another two 60,000 CFM dust collectors in parallel fashion. These latest additions serve the cleaning and grinding operations and also include the current versions of broken bag detection, variable frequency drives, PLC controllers with modern HMI panels, and a major upgrade to a Teflon membrane-type filtration system. This filtration approach allows the particulate to slide off of the bag more readily, thus reducing the requisite pulse frequency and duration. The result of this filtration system is improved efficiency and effluent air quality while decreasing compressed air usage by roughly 75%.
Over ninety-nine percent (by weight) of all waste leaving our facility is either recycled or beneficially reused. Also, our on-site operations are ninety-eight percent below our regulatory limit for the emission of carbon dioxide. This is without considering the 200+ acres of forest now being managed in conjunction with the US Department of Agriculture.
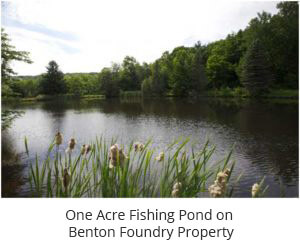
Benton Foundry has been in continuous operation since the mid 1800′s and rests in a rural setting on over 200 acres of land 5 miles outside the town of Benton, PA.
ADDITIONAL GREEN PROJECTS
- Taking a “mass balance” approach to material selection under the thinking that if we can use environmentally benign products in our process, then we do no harm. The sourcing of raw materials is accomplished in a safe, local, and responsible manner.
- Partnering with CPower participating in their Emergency Load Response Program and Synchronous Reserve Program reduces power consumption during stressful periods within the PJM electrical grid. This approach reduces our consumption, thereby reducing cost and our environmental impact. Thus, we recognize our corporate responsibility in times of stress and need.
- Adopting Customized Energy Solutions software for electrical Demand Control and Demand Response efforts. This initiative has considerably reduced our power consumption. Our capacity transmission charge was reduced by over 2,500KW. This is a savings to the PJM grid as well as to Benton Foundry.
- Adopting the exclusive use of super-efficient motors throughout the facility to minimize electricity consumption. Although we realize that the motors may be slightly more expensive, they will pay for themselves many times over.
- Installing new variable speed compressed air equipment with automated controls to maintain constant air pressure throughout the facility. This equipment also includes condensate drains, air tanks and low pressure-drop filters.
- Installing a crusher to densify our metallic charge material. The increased furnace charge density requires less energy to melt. Another advantage includes a reduction of furnace charge time which also reduces the amount of time the furnace lid stays open during charging. Additionally, safety was increased by reducing the risk of furnace bridging from interlocked and stringy charge material. Other benefits include cleaner charge material, lower scrap, larger magnet capacity and reduced storage volume.
- Maintaining a Beneficial Reuse Permit for our residual waste.
- Recycling wood, cardboard, plastic, aluminum and other scrap metals, along with shredded paper to local farmers for animal bedding.
- Implementing the use of causticized lignite in our sand system to reduce our emissions.
- Adoption of LED lighting, harvesting of outside light and motion sensors.
- We’ve installed 1.6 acres of engineered wetlands in a High-Quality Watershed on our property. We also replaced the existing riparian buffer to the native trout stream that was diseased and dying with a robust and disease resistant engineered riparian buffer. We added a 0.71-acre rain garden designed to mitigate the sediment from our parking lot before recharging the runoff to groundwater. We flanked our trucking area to one side with a 2.7-acre vegetated swale and the other with a 0.25 acre amended soil zone to accomplish similar results as the rain garden with increased diversity. We also added stormwater-quality filters, several check dams, and an underground water retention basin along with filter bags at our storm drains all in an effort to recharge the groundwater supply with more high-quality water. In summary, we have been able to decrease the amount of rainwater runoff as opposed to the expected increased runoff due to the additional buildings and paved areas. This aspect of the expansion was coordinated with the Army Corps of Engineers, PA Department of Environmental Protection, the local Conservation Districts and others with a cost of around $500,000.
- As a result of some of the projects highlighted above, Benton Foundry won the American Foundry Society 2022 Green Foundry “Sustainability & Stakeholder Engagement” Award.
- Benton Foundry has also been recognized as the 2023 “Metal Caster of The Year”.