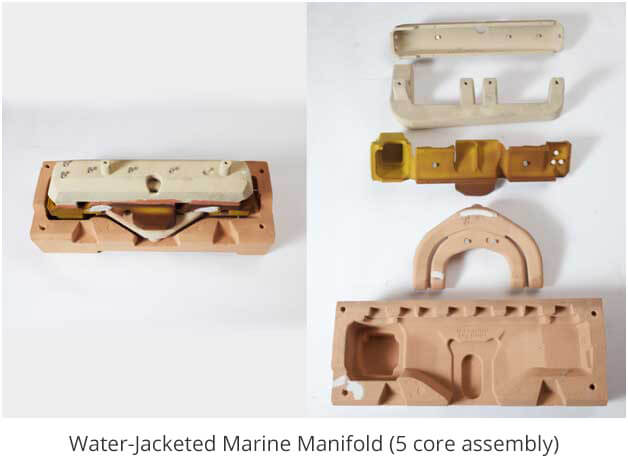
A problem to remedy, a puzzle to solve, a part to build. Superior design and problem solving are crucial for superior results, from prototype through production and delivery. Whether you come to us with a sketch on a napkin or a 3D CAD rendering, we help develop and refine your design to take advantage of all the benefits of iron casting. How does the part need to be made? How many cores are required? How are the cores held in place? Does draft need to be added? Are there isolated heavy sections, and, if so, how can we address them so they stay solid? Can the design be improved to reduce or simplify machining? We find and fix problems before they have a chance to become problems.
Through our design process, we identify how to make the job easier, less expensive and more efficient. Design reviews, 3D modeling, solidification analysis and rapid prototyping are just a few of the services we offer. Additionally, we will assist in converting forgings and weldments to cast parts which can significantly reduce the cost of your project. The earlier you get Benton’s team involved, the smoother the prototype, sample and approval process will go in order to get the job into full production.
How can we begin? In a perfect world, the following information initially would be helpful in expediting your castings. We realize that this information is not always readily available. Provide what you can. We will work with you from design through to delivery.
- A model or drawing to the current revision level. In absence of the aforementioned, reverse engineering a casting may be an alternative.
- Casting number and/or part number in addition with where on the casting the part number, foundry ID and heat date should appear.
- Revision date and/or revision level. If the part is being revised, then a detailed notation specifying the exact change needed.
- Grade of Iron.
- Heat treat specification, if any.
- Rough casting weight.
- Annual volume and anticipated order quantity.
- Areas to be machined and the amount of machine stock required.
- Datums and fixturing locations for machining.
- Desired parting line and draft angles.
- Tolerance of angles, radii and dimensions.
- Location on casting to verify hardness.
- Special notes and critical characteristics.
TESTING & INSPECTION REQUIREMENTS | SPECIFICATIONS |
---|---|
An itemized list of testing and inspection requirements you require on samples and on production lots will also be needed. The following are available, however, as the requirements increase, so does the cost.
|
Licensed Software:
|
Magmasoft Solidification Analysis | |
Articles |